Stainless steel drums for hygiene-sensitive applications that set new standards
Increase quality & safety by minimizing particle adhesion
- Contamination-free production: Stainless steel surfaces from BOLZ INTEC are optimized for industries with the highest demands on hygiene and cleanliness.
- Reproducible product quality: Stainless steel surfaces from BOLZ INTEC are flawless and reduce the risk of production downtime & product recalls.
- Compliance with the highest standards: Stainless steel surfaces from BOLZ INTEC guarantee compliance with GMP and EHEDG standards.
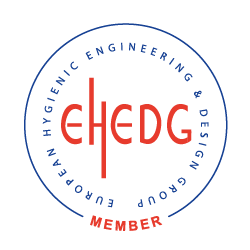
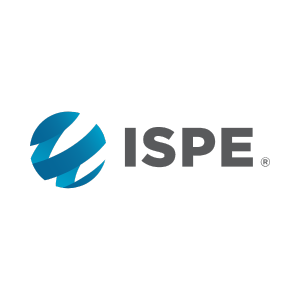
The right stainless steel drum for every substance
Whether powder or granulate, whether pasty or liquid media: any substance can be stored and transported absolutely safely in a stainless steel drum from BOLZ INTEC. Our stainless steel drums meet the specific requirements of the pharmaceutical, biotechnology, fine chemicals and cosmetics industries and are suitable for use in hygiene-sensitive areas.
For the pharmaceutical and chemical industries, BOLZ INTEC offers stainless steel lidded drums that guarantee maximum protection for pasty, liquid or solid products.
All stainless steel drums are manufactured in accordance with the current GMP standard and DIN EN ISO 9001:2008 and can be supplied in both individual and series production - naturally in perfect quality, because BOLZ INTEC fulfills almost every customer requirement thanks to its precise and flexible production methods.
The chrome-nickel steel materials used are rust-free, light-resistant, odorless, tasteless and diffusion-resistant. The lidded drum is also easy to clean and 100% recyclable. Reusable lids, seals and clamping rings seal the lidded drum airtight.
We provide you with sample barrels and barrel rollers free of charge for testing.
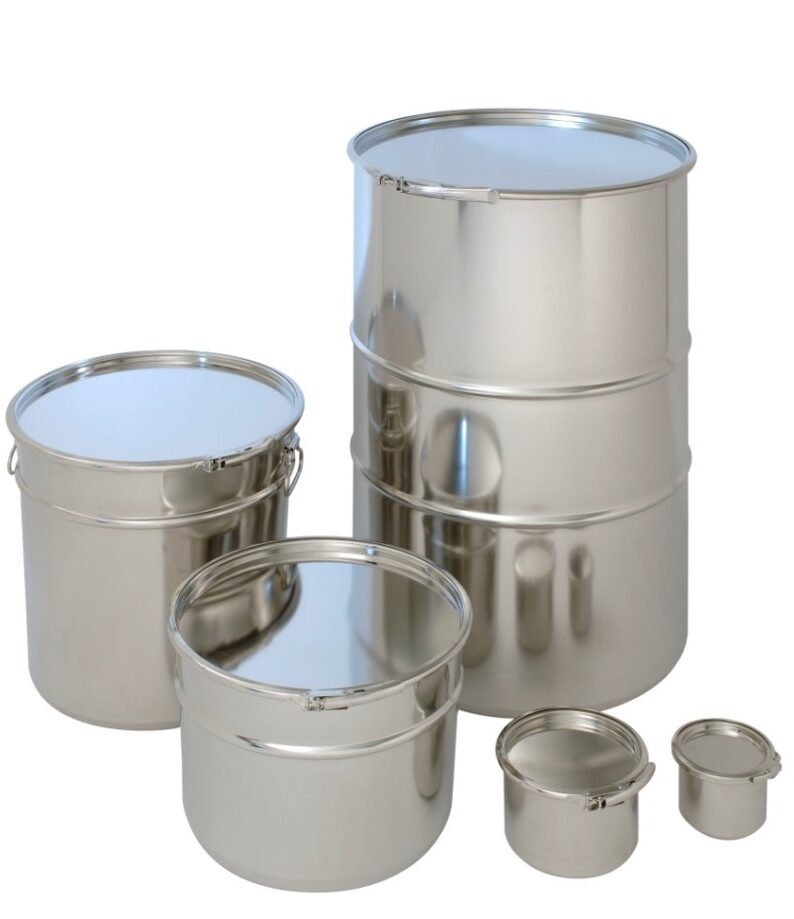
Ra < 0,05 µm ist die Oberflächenrauheit von Fässern mit dem Optimized Grind Finishing von BOLZ INTEC
Types of stainless steel drums from BOLZ INTEC
Lidded drum SKE-1-632
Lidded drum SKE-1-633
Lidded drum SKE-1-671
Stainless steel drums from BOLZ INTEC have the following features
10 years shelf life due to barrel repair
Stainless steel
Light & UV-resistant
Inert & odorless / tasteless
Diffusion-proof
100 % recyclable
Reusable clamping ring cover
Simple & airtight sealing
Seals with FDA approval
Deep-drawn base & lid
Jacket & base butt-welded
Seams rolled flat & finely sanded
Materials for stainless steel drums
1.4301 (AISI 304)
Corrosion-resistant austenitic steel, versatile, good weldability, suitable for chemical and food applications.
1.4404 (AISI 316L)
Austenitic steel with added molybdenum for high corrosion resistance and good weldability, versatile in use.
1.4435 (AISI 316L)
Austenitic steel with increased molybdenum content and low ferrite content (< 3 %) for improved corrosion resistance and higher resistance to pitting.
1.4539 (AISI 904L)
Heat-resistant, high-alloy steel with increased chromium and nickel content, excellent resistance to acids and corrosion at high temperatures.
2.4602 Hastelloy C22
High-alloy nickel-chromium-molybdenum steel, excellent corrosion resistance to aggressive media such as acids, chlorine and oxidizing substances.
Special materials
In addition to the materials mentioned, BOLZ INTEC also processes other materials, depending on the customer's specifications and requirements.
Surfaces for stainless steel drums
Mill finish / 2B
Standard surface after rolling, uniform smoothness and roughness for a wide range of applications.
Brushed
Matt finish thanks to brushing, increased scratch resistance, ideal for aesthetic and functional applications.
Ground to
Ra < 0.4 µm
Fine, even surface, especially for applications with high purity requirements and aesthetic demands.
Electropolished up to
Ra < 0.25 µm
High-gloss finish thanks to electrochemical polishing, maximum corrosion resistance and surface cleanliness.
OGF process up to
Ra < 0.05 µm
Optimized Grind Finishing is a process developed by BOLZ INTEC and the University of Constance for minimal particle adhesion.
The right stainless steel drum for every purpose - options for individual customization
Flare ring & reducer
Handle variants & edging
Dosing units & inlet pieces
The right accessories for every drum from BOLZ INTEC
Barrel rollers & barrel trolleys
Drum emptying system
Transport & emptying system (EPS)
Stainless steel drums from BOLZ INTEC
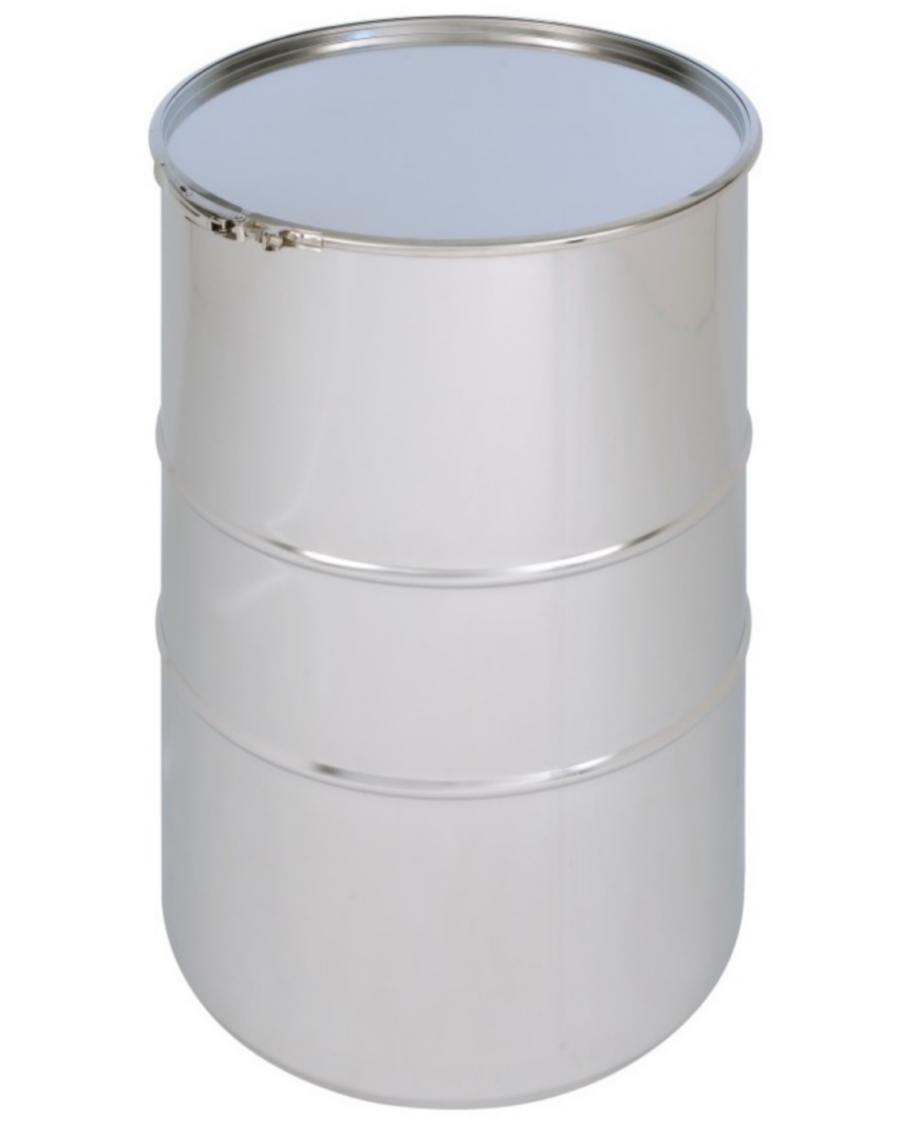
Barrel trolley
Barrel tipper
Barrel pallet
Pharmaceutical flaps from external partners
Funnel adaptation symmetrical or asymmetrical
Slip lid up to ⌀ 250
Lid with superstructures
Drum lifters from external partners
Drum washing machine from Simoflex GmbH
Drum mixers from external partners
Barrel roller
The Optimized Grind Finishing process (OGF)
In the pharmaceutical, chemical and food processing industries, minimizing build-up in containers is a critical factor for efficiency and quality. The build-up of substances on the inside walls of containers can lead to increased cleaning effort, product losses and contamination. This costs money and ties up resources. Especially in industries where EHEDG (European Hygienic Engineering & Design Group) certification and hygienic design are becoming increasingly important, minimizing adhesion has become a critical factor.
Research carried out by BOLZ INTEC in cooperation with the University of Constance has shown that the way in which stainless steel surfaces are removed plays a key role in minimizing adhesion. Different grinding methods result in different adhesion behavior, despite the same Ra values, and the OGF process from BOLZ INTEC leads to a lower adhesion of particles.
Below is a scanning electron microscope image of the stainless steel surface after electropolishing and Optimized Grind Finishing, as well as images of the surface texture roughness data and repeatability.
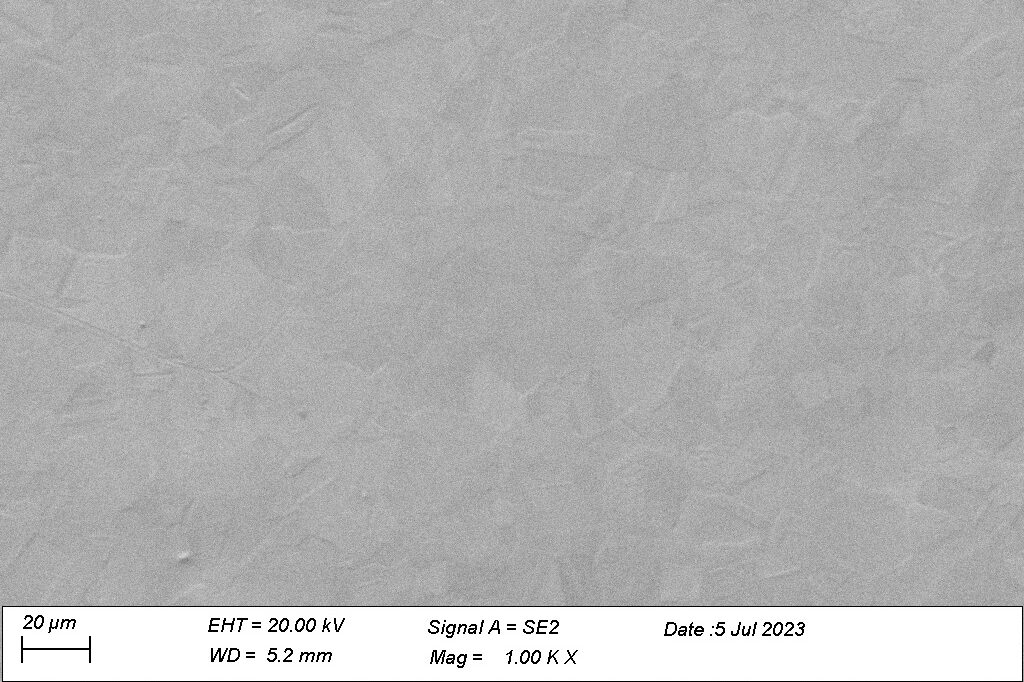
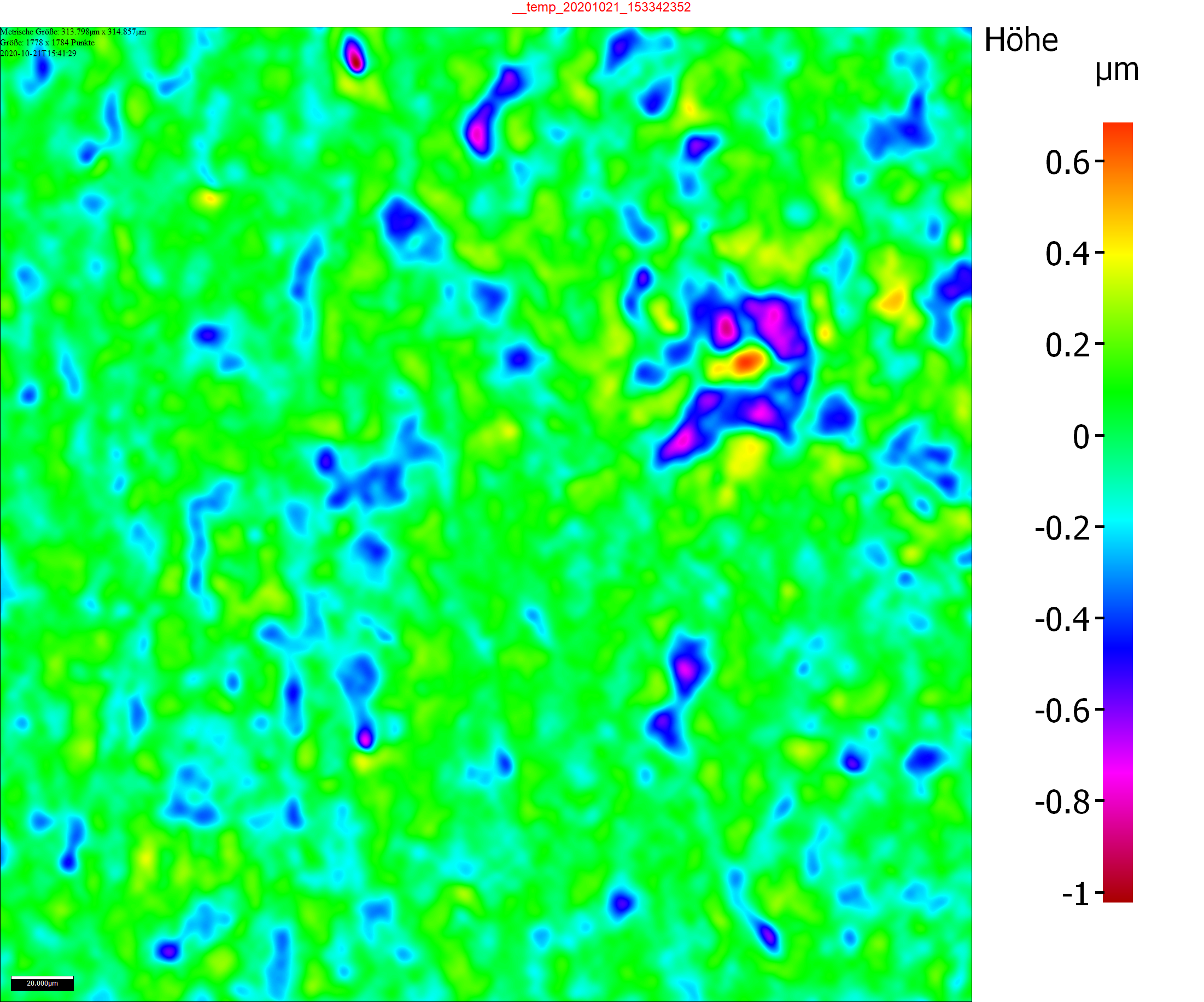
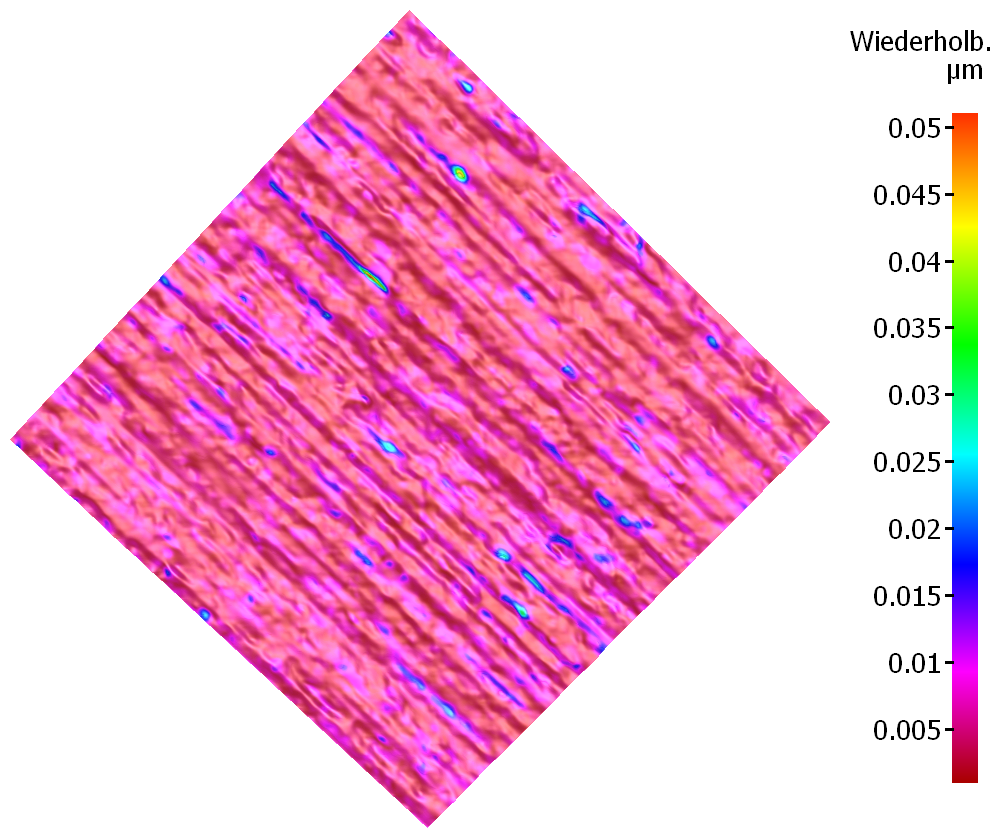
Easy cleaning & minimal adhesion
The Optimized Grind Finishing (OGF) process leads to a low adhesion of particles on the surfaces of the containers. This significantly improves cleaning efficiency and reduces the risk of contamination of product batches.
Reproducible surface quality
The OGF process enables reproducible surface quality. In contrast to conventional processes, in which variable factors such as manual contact pressure or the quality of abrasives play a role, the OGF process offers consistent surface quality.
Visual aesthetics and low number of errors
The stainless steel surfaces treated with the OGF process have an attractive appearance and defects in the surface structure are significantly reduced thanks to the fine and gentle removal process. This is particularly important in industries that place high demands on safety.
Improved corrosion protection
The electropolishing process not only improves the optical quality, but also results in chemical changes that lead to improved corrosion protection. This is particularly relevant for applications in chemical and pharmaceutical processes.
Reduced risk of batch contamination
The improvement in cleaning behavior through the OGF process leads to a significant reduction in residual dirt adhesion in the containers. This significantly reduces the risk of contamination between different product batches.
Applicability in critical industries
The process is seen as particularly advantageous for critical industries such as nanotechnology or biotechnology and pharmaceutical technology, where the highest purity requirements and the avoidance of contamination are of crucial importance.
Increased efficiency through minimal adhesion
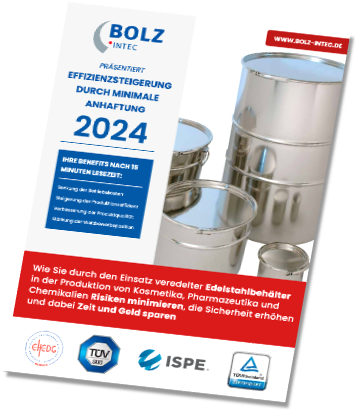
Simply send an e-mail and receive the download link
Services from BOLZ INTEC
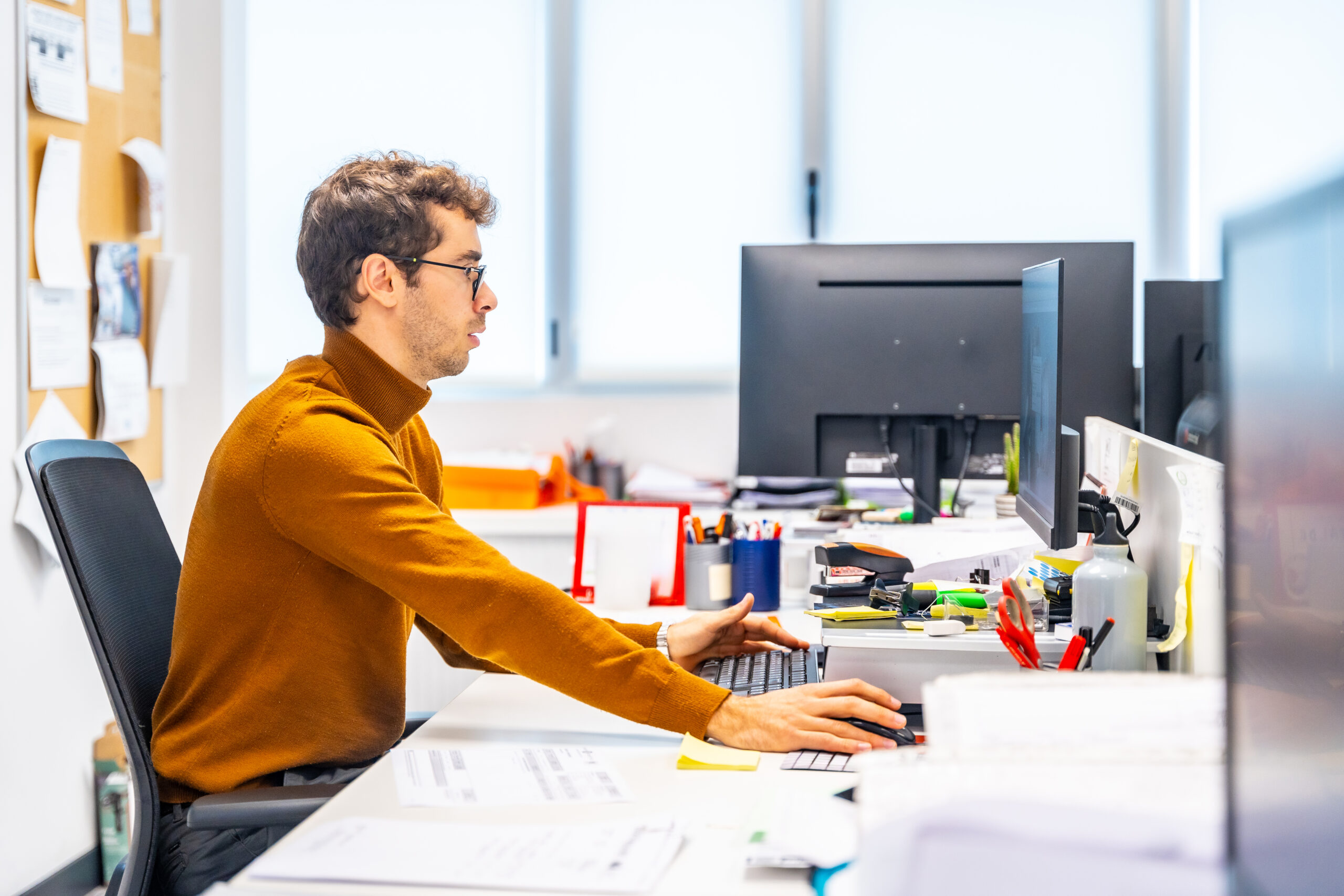
Technical advice & design
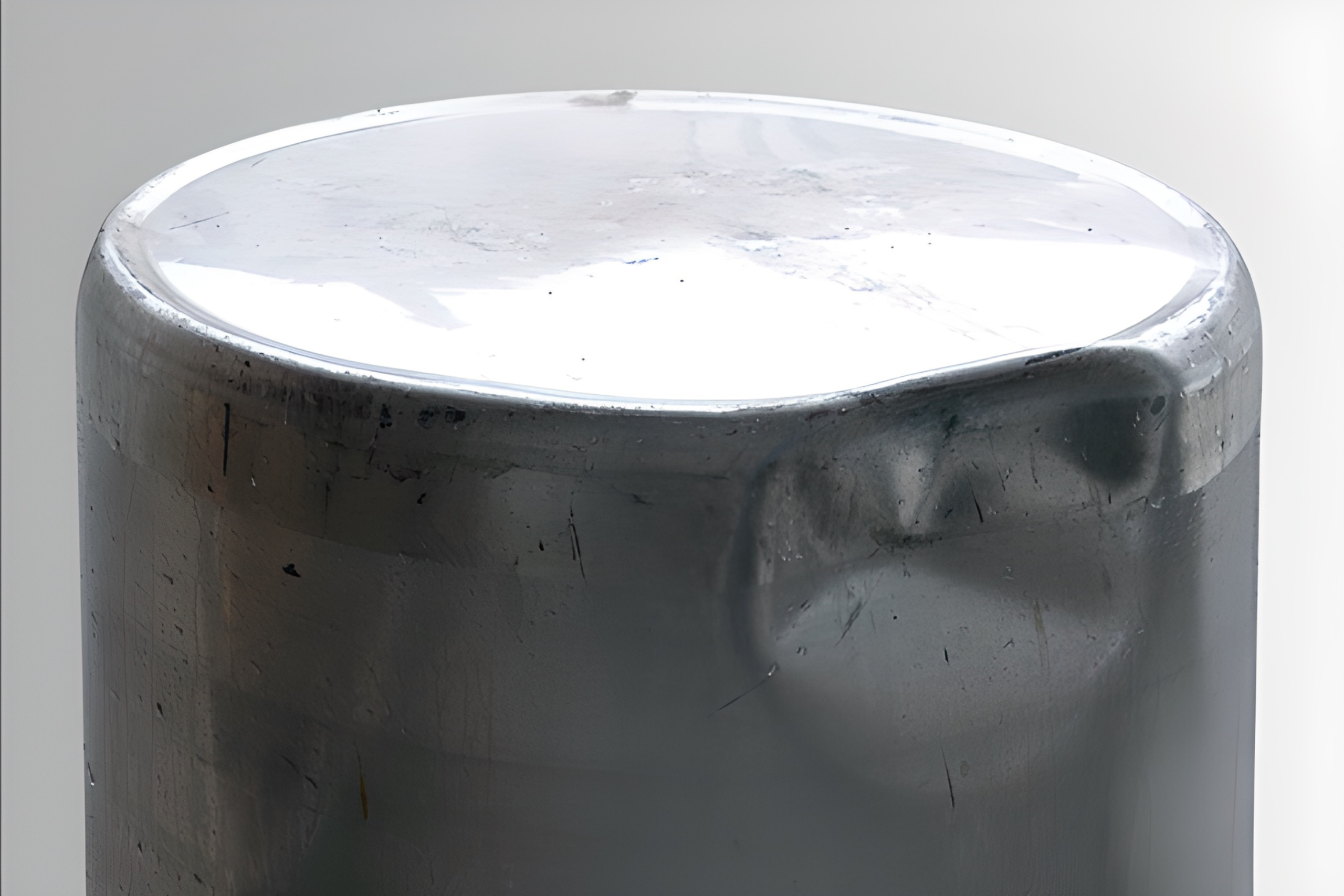
Barrel repair
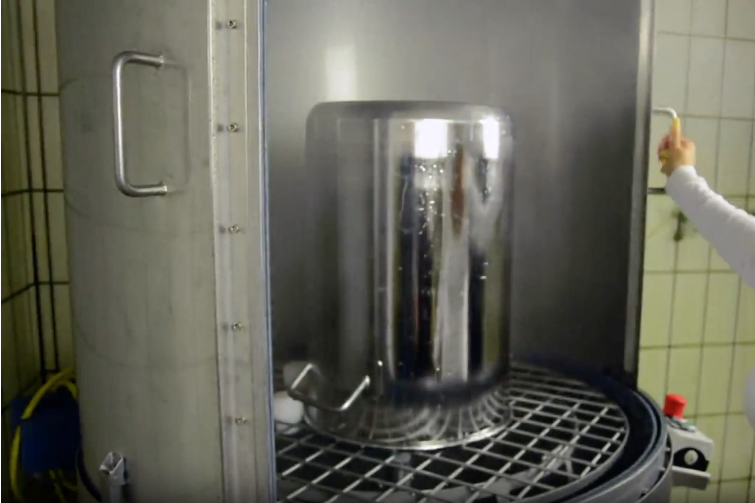
Simoflex® drum wash

Electropolishing
Why customers around the world choose our stainless steel drums
Tradition & innovation since 1919
BOLZ INTEC specializes in the manufacture of stainless steel drums, pressure vessels, agitator vessels, transport containers and transfer systems for hygiene-sensitive industries.
High vertical integration
BOLZ INTEC has acquired outstanding expertise in the machining of stainless steels and special materials such as Hastelloy. Combined with the skills and abilities of our team, this enables us to achieve maximum vertical integration. All production steps are carried out in-house. BOLZ INTEC is therefore able to react extremely flexibly to customer delivery date requests and guarantee unique quality.
Customized solutions
Our design department designs, plans and develops practical products according to our customers' requirements. These include, for example, containers for pasty substances or liquids, transport containers for UN hazardous goods, cans for the storage and transfer of active ingredients, suction hoods for dust-free container loading and much more.
One-off production & small series
BOLZ INTEC also manufactures custom-made products and small series.
Machines for perfect surfaces
Nothing in the BOLZ INTEC machine park is off the shelf. From the deep-drawing press to the electropolishing system, we work with special machines that have been developed according to our own specifications in order to meet the highest standards of quality and precision.
Traceability & reproducibility
BOLZ INTEC's QM system and our intensive testing procedures ensure the consistent quality of the stainless steel surfaces manufactured by BOLZ INTEC. In this way, we make a decisive contribution to the traceability of products in critical industries.
Trust & security
Our striving for perfect quality, state-of-the-art production methods, but also craftsmanship and know-how are the basis for the superior BOLZ INTEC quality, which means safety and reliability for our customers. It is therefore not surprising that 80% of our customers have reordered every year for the last 10 years.
Comprehensive certification
We regularly have our quality certified externally: DIN 9001:2015, DIN EN ISO 3834-2:2006-03, DIN EN ISO 115085-2/CL1. We are a specialist company according to WHG §19/1 and carry out process tests according to DIN EN ISO 15614-1, operator tests according to DIN EN 1418. BOLZ INTEC fulfills the Pressure Equipment Directive-2014-68-EU/AD-2000 HPO and employs Intern. Welding engineers (DVS/IIW 1170).
High efficiency, low costs & great economy
Time savings in production
The use of stainless steel containers with optimized surfaces leads to significant time savings in the production process. By minimizing the build-up of materials, cleaning and maintenance times can be drastically reduced. This enables the containers to be reused more quickly and increases the overall efficiency of the production lines. In a production-intensive environment where time equals money, this time saving represents a significant economic advantage.
Reduced risk of production downtime
The reproducible quality of the stainless steel surfaces and the reduced number of defects minimize the risk of production downtime due to surface problems. This can lead to higher overall productivity and less downtime.
Reduction of production losses
Optimizing the container surfaces also minimizes the amount of product loss. Reduced adhesion means that more of the material produced is available for its intended use and does not end up as waste. This is a particularly important factor in industries where high-quality or very expensive materials are processed.
Improvement of product quality & product safety
Contamination-free production results in a higher quality end product. This is crucial in industries with strict quality and purity requirements, such as pharmaceuticals and food production, where purity and safety are top priorities. The use of optimized stainless steel containers can therefore also lead to improved brand image and customer satisfaction. We ensure the quality of our containers through our QM officer and stringent production processes. You will receive the corresponding documentation for each of our stainless steel drums.
Cost reduction through efficient cleaning & barrel maintenance
In addition to saving time, optimized surfaces also lead to a reduction in the costs of cleaning processes. Less build-up means less need for cleaning agents, water and energy. There is also less wear and tear on the containers themselves, which increases their service life and reduces the need for new purchases. In the long term, these savings in operating costs can make a significant difference to a company's profitability.
Longer container service life & positive eco-balance
The improved corrosion protection provided by the electropolishing process helps to extend the service life of stainless steel containers. Customers can thus reduce their costs for replacement investments and maintenance.
Customers from these industries increase their efficiency with stainless steel drums from BOLZ INTEC
Reach your goal in just a few steps
Request
Send us an e-mail, give us a call or book an appointment via Calendly. In a phone call with one of our competent contacts, we will clarify a few questions in advance using checklists and send you a non-disclosure agreement (NDA).
Test phase
Based on your objectives and specifications, you will receive drums, containers, funnels and accessories from our test center - as required - to try out and test. You can use your test equipment to verify or adapt the specifications of your request.
Offer
During a visit to your premises, our competent contact partners will advise you on clarifying any final questions, finding solutions to identified problems and defining your exact requirements. We can then start production.
Our project team looks forward to your inquiry
Do you have questions about our products and services or would you like advice from one of our competent employees?
Give us a call or send us an e-mail. We will make time for you and will be happy to call you back if you wish.
You ask, we answer
Our stainless steel containers and appliances are used in various industries, including pharmaceuticals, chemicals, food, cosmetics, energy and environmental technology, aerospace, as well as research facilities and laboratories.
Our stainless steel containers are available in a variety of sizes and capacities to meet the individual requirements of our customers. Contact us for customized solutions.
We offer customized solutions and adapt our stainless steel containers to individual requirements, such as process parameters, volumes and special functions.
Our services include electropolishing, mechanical processing and the unique Optimized Grind Finishing (OGF) process for optimum surface quality and minimal particle adhesion.
Our containers meet the strict hygiene standards of the EHEDG (European Hygienic Engineering & Design Group) and are therefore ideal for use in hygiene-sensitive sectors.
Our experienced team offers comprehensive advice and support for the seamless integration of our stainless steel containers and appliances into existing production processes.
The maintenance requirements for our stainless steel containers and appliances are minimal. Regular inspections and, if necessary, cleaning are sufficient. Our stainless steel tanks are durable and robust and, if the worst comes to the worst, we offer our customers repair services.
Our optimized stainless steel containers offer better cleaning properties, lower particle adhesion and meet the highest hygiene and cleanliness standards.
Our stainless steel containers are resistant to aggressive chemicals and are perfect for safe storage and transportation in the chemical industry.
The surface finish has a decisive influence on the chemical and physical properties of stainless steels. In hygiene-sensitive sectors such as the pharmaceutical, cosmetics and food industries, technical terms such as EHDG or hygienic design are becoming increasingly important. The background to this is that operators want to avoid the carry-over of particles and the associated contamination of their batches as far as possible. One of the decisive factors here is the cleaning behavior of surfaces and the associated adhesion behavior of particles.
BOLZ INTEC, a long-standing producer of containers and special constructions made of chrome-nickel steels, has asked itself precisely these questions and has investigated the properties of surfaces in several years of research work in cooperation with the University of Constance. In addition to the usual roughness profile of surfaces, which is currently used as the main feature when describing surface quality, attention was paid to other factors such as their final surface energy and examined in more detail.
The current state of the art is the assessment of surfaces using non-destructive testing, such as roughness depth measurement in conjunction with optical testing. However, in addition to these, there are other criteria that should not be ignored. Among other things, the way in which the surface is finished should be considered. It has been found that different grinding methods show different adhesion behavior in the final assessment of the surface, although the Ra value of both surfaces is the same. This means that the way in which the material is removed plays an important role here. As an experiment, the container was ground with an automated grinding process over a long period of time, in contrast to the usual manual grinding. This fine removal over a longer period of time resulted in less adhesion and therefore better cleaning. In the further course of the investigation, this was referred to as the final surface energy.
BOLZ INTEC has made use of the knowledge gained from the research cooperation with the University of Constance and developed a process in which the low and constant removal of the stainless steel surface is achieved semi-automatically over a long period of time. The process is called Optimized Grind Finishing or OGF process. The removal in the container is achieved with geometrically indeterminate grinding wheels that move inside the container. The major advantage of the OGF process is that, in addition to its outstanding quality, the surface is reproducible. The result is independent of undefined variables, such as the manual contact pressure during conventional grinding by an employee or the quality of the abrasives.
In the course of the investigations in cooperation with the University of Constance, BOLZ INTEC has further refined stainless steel surfaces refined using the OGF process and subjected them to an electropolishing process. In this process, the peaks in the surface structure are further removed, which, in addition to optical advantages, also brings chemical changes, such as improved corrosion protection through a reinforced passive layer. In the final assessment of the study, the improved cleaning behavior was demonstrated with the help of a test based on VDA19.1 (March 2015)/ISO16232 (December 2018). The OGF process drastically reduces residual dirt adhesion in containers and thus offers the operator the added value of significantly reducing the risk of contamination of two batches.
With the help of research, BOLZ INTEC has generated a surface whose roughness profile and optical assessment can be produced with repeat accuracy. In addition, this surface has advantages over the reference model in terms of cleaning. This added value can be decisive, especially for critical, very valuable or very fine particles. Examples include industries such as nanotechnology, biotechnology and pharmaceutical technology or all others where batch purity and the avoidance of contamination is a decisive factor in production.
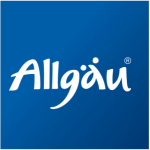
Do you have questions or are you looking for advice?
Please do not hesitate to contact us by phone or e-mail.